Improving safety in picking processes
Digital Tracking Towers and simulation tools can be quickly used, by an appropriate data, to make sure warehouse resources maintain a physical separation of six feet or not. The simulation tools can use several delivery items, bins and work-centres to mimic the path of operators within the warehouse. Thus, we can calculate the maximum number of warehouse users a site can have without compromising operational efficiency and safety guidelines.
Because of longer transit times and labor shortage, due to social distancing, stock accuracy is now more critical than ever. Rather than having teams sweeping racks and shelves to take a stock count, firms might explore an approach of combining physical inventory counting with either picking or put away activities. Subsequently, we will reduce the number of people having access to products and bins.
SAP EWM offers a picking process that can be highly recommended for pickers working with the threat posed by the virus, the “Pick, Pack and Pass Process”.
For example, by breaking the picking process into multiple activity areas, we can assign a resource to each aisle. As soon as a picker has selected a warehouse order, he passes on the goods, using a conveyor belt. Thereby, we will be able to achieve efficient picking with proper social distancing within the warehouse.
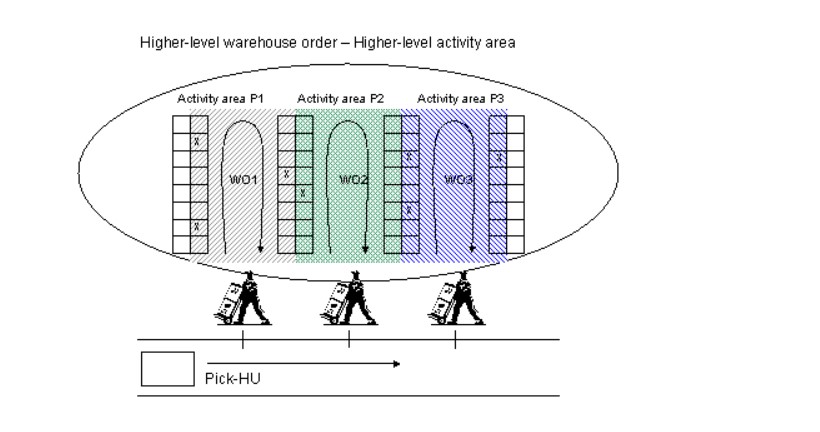
Source: example of the ‘pick, pack and pass process’ – SAP EWM
Warehouse planners are facing multiple challenges that will require them to rethink safety measures, including the requirement to close for regular cleaning and rearrange break rooms. By combining machine learning and location data, new algorithms can be developed to avoid congestion and predict any possible contamination spots.
Regardless of the current situation, companies should rethink their warehousing and logistics operational processes so making them safer and more resilient beyond the immediate challenges of COVID-19, future-proofing against future risk.