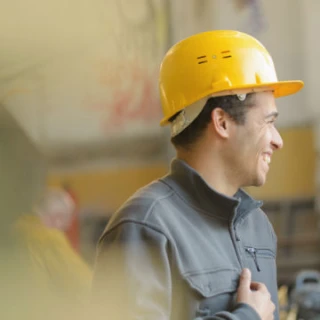
Resolving three key manufacturing challenges with process optimisation
- finance
- discrete manufacturing
The UK Manufacturing sector continues to grow, even in uncertain times around Brexit. It is currently the 9th largest globally and contributes to a huge 44% of the UK exports. Rapid growth has resulted in successes and struggles, bringing about concerns faced by few other industries as a whole.
To continually grow as they have done in the past, discrete manufacturers have to conquer adversity, dealing with unique challenges. In this first blog of a three-part series, we’re looking at the key challenges in the industry and how technology can be used to address these issues.