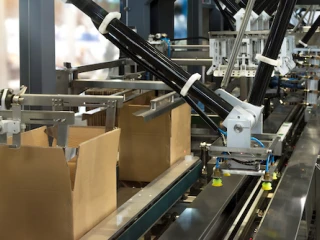
Imagine a time when you can…
- Decrease days in inventory by integrating scheduling and execution for a consistent view of inventory and product data.
- Minimize disruptions in production due to changed routings, work instructions, or production orders while aligning with shop floor execution.
- Reduce manufacturing cycle time by adjusting production schedules to work with current plant conditions.
- Reduce revenue loss from stock-outs through fast and responsive production planning scenarios.
- Increase manufacturing efficiency with less wastage in terms of materials, time, and energy.
- Always have materials and components ready for production when needed.
With SAP, the time is upon us. SAP covers Plan-to-produce: from forecasting, sales and operations planning, demand management, master production schedule, material resources planning, manufacturing execution, to order settlement. Plan-to-Produce integrates with Finance, Sales, Procurement, and Inventory modules.